How to cut acrylic sheet
As a new material, acrylic sheet is widely used in advertising printing, furniture cabinets, display boxes, aquariums, building templates and other fields. For JUXIN Plastic Group, we mainly produce acrylic sheets and export high-quality sheets to many overseas customers. As for the application and processing of acrylic sheets, there is no doubt that acrylic sheets must be cut. Today Juxin Plastic Group will recommend various cutting methods and their advantages and disadvantages(How to cut acrylic sheet?).
Acrylic cutting can be divided into two cutting methods: manual and mechanical. Among them, hand cutting tools such as hand knives, hook knives, and plywood knives are more suitable for personal processing. Mechanical cutting methods include: electric saws, vibrating cutters, milling cutters, water jets, lasers, CNC engraving, etc., which are more suitable for batch processing by some manufacturers or companies. Whichever method you choose, you need to choose the right tools and materials and follow the correct procedures.
We generally choose different processing methods according to the thickness of the acrylic sheet to cut the acrylic plate to size.
1)Handmade knife:
If you use a handmade knife to cut, it is generally suitable for thin acrylic sheet. Use a ruler to measure and mark the size of the acrylic to be cut. Use a hand knife to repeatedly draw a straight line on both sides of the acrylic plate, and gently break the acrylic along the straight line with your hands.
2)Hook knife:
More suitable for thicker acrylic sheets. Get your hook knife and ruler ready, measure and mark where you need to cut. Then, use the hook knife to gently cut to half of the board, paying attention to maintaining strength and accuracy. Finally, gently break off the remaining boards with your hands and polish them if you want the edges to be neat. This method is suitable for cutting small areas and can save cost and time.
3)Plywood knife:
① Press the ruler on the acrylic board that needs to be cut, and use the plywood knife to draw a straight and thin groove on the acrylic board.
② Place the acrylic board with the straight groove on it at a right angle.
③ Align the linear groove of the acrylic plate with the edge of the workbench on the side of the workbench
④Press down with your hand, and the acrylic plate will immediately break neatly along the linear groove.
1)Electric saw:
An electric saw can cut through acrylic sheets quickly. Thick acrylic sheets are generally cut with an electric saw. You need to use a stainless steel saw blade with serrations. The speed must be low. If the speed is high, the acrylic board will melt. A jigsaw is best, and a hacksaw can also be used, but the cutting surface is relatively small. big.
2)Vibrating knife cutting machine:
The vibrating knife cutting machine uses a blade for cutting. According to the thickness of acrylic, you can choose a milling cutter, a vibrating knife, or a starting knife. Among them, the milling cutter has the best cutting effect, with exquisite cutting arcs, and the cutting efficiency is faster than that of the laser cutting machine.
The vibrating knife cutting machine uses the blade to vibrate up and down for cutting. Computer control can cut any shape. The vibrating knife cutting machine is suitable for cutting acrylic sheets less than 5mm. If it is thicker, it will cause the knife to jump. In addition, the vibrating knife cutting acrylic will produce a circle.
The pattern phenomenon of the circle requires secondary processing. This is because the knife vibrates up and down at the same time during movement, causing uneven cutting.
3)Milling cutter cutting machine:
The milling cutter cutting machine can be used for cutting thicker acrylic plates. The cutting surface is smooth and does not need to be polished again. The cutting speed is proportional to the milling cutter speed. You need to select the speed according to the actual thickness, otherwise it will cause damage due to too fast speed. Material melts.
4)Waterjet cutting:
Waterjet cutting is an innovative material cutting technology that uses high-pressure water flow to accelerate water to extremely high speeds, forming a high-energy beam water cutting capability. This technology has the advantages of high precision, high efficiency, and low pollution, and is widely used in cutting acrylic sheets.
5)CNC engraving machines:
CNC engraving machines have unique advantages in cutting acrylic sheets. With the popularity of CNC engraving machines in recent years, more and more businesses choose to use CNC engraving machines to cut and engrave acrylic panels.
The acrylic plate CNC cutting machine is an efficient and precise CNC cutting equipment. The engraving machine can finely cut various materials and can cut various irregular-shaped materials.
The main application fields of CNC engraving machines in the engraving and cutting of acrylic plates include crystal. Letters, display cabinets, fish tanks, acrylic signs, etc.
Acrylic plate CNC cutting machine is mainly composed of CNC system, computer, processing head, etc. The CNC system is the core of the equipment, capable of automatic control and optimization, and controlling the depth, speed and direction of the cutting process.
The computer is the control center of the equipment and can realize graphical interface operation and data processing. The processing head is the cutting tool of the equipment, which cuts the material through high-speed rotation.
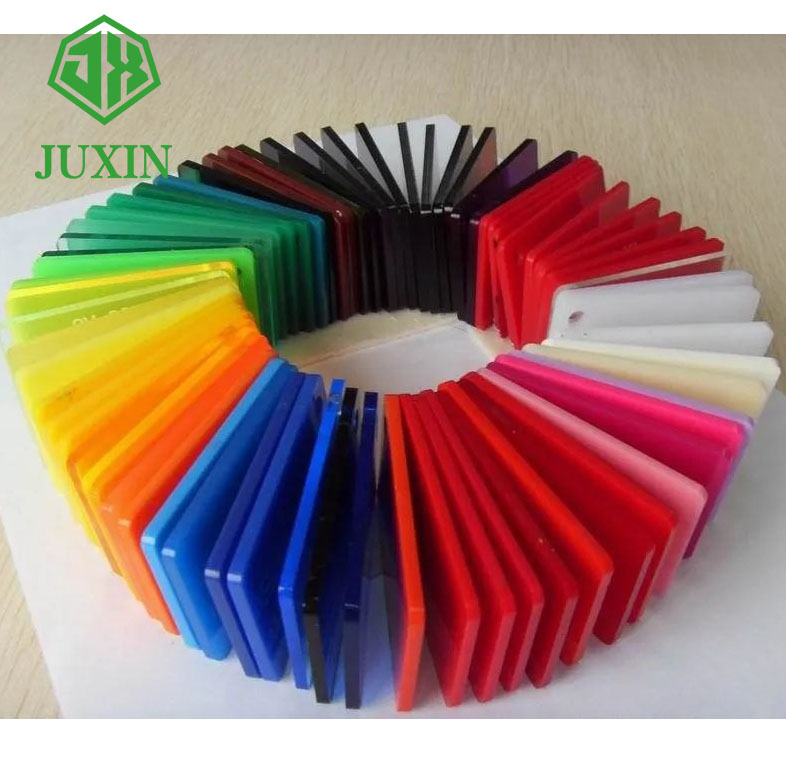
(1) Before processing, it is first necessary to initialize the equipment, including setting parameters such as cutting speed and depth.
(2) Place the acrylic plate to be cut on the platform of the cutting equipment, and adjust the position of the equipment and the direction of the tool to make it suitable for the material to be cut.
(3) Start the computer and CNC system to perform graphical interface operation and data processing. According to the shape and processing requirements of the acrylic plate, set the cutting parameters, such as cutting speed, depth, direction, etc.
(4) Start the processing head and start rotating and cutting the material at high speed. The CNC system automatically controls and optimizes the depth, speed and direction of the cutting process according to the set parameters, thereby achieving precise cutting.
(5) When the cutting is completed, the CNC system will automatically stop the rotation of the machining head and take out the cutting part.
For acrylic sheets of different thicknesses, different cutting processes are required. For example, for a 0.1 mm acrylic sheet, a single layer cutting is required; for a 0.5 mm acrylic sheet, a double layer cutting is required; for a 1 mm acrylic sheet, a three layer cutting is required. For the cut acrylic plate, subsequent processing such as grinding and polishing is required to improve the processing accuracy and surface finish.
(6) Laser cutting:Acrylic sheet for laser cutting is a precise and efficient cutting method that cut acrylic sheets quickly and accurately.
Laser cutting machines are thermal melt cutting, which may produce burnt and yellow edges during the cutting process. You can use auxiliary gas or a ventilator to absorb the smoke generated during cutting in a timely manner. Laser cutting machines can cut various complex shapes accurately and efficiently.
Acrylic cutting is common in laser processing because acrylic is a common material for this application. However, getting a nice cut can sometimes be a problem, especially with thick acrylic.
1.Use a focusing mirror (4 inches)
If the standard lens of the laser machine is 2 inches, then the recommended maximum thickness of the acrylic is 10 mm. If you want to cut acrylic with a thickness of 15mm or 20mm or even thicker, you need to use a 4-inch lens to achieve this.
2. Minimize the blowing of the pen carriage as much as possible
When cutting thick acrylic, if the flame goes out on the acrylic, it may be that the laser is not powerful enough to cut the acrylic completely, or it is too fast.
If you are cutting thick acrylic, you will need to cut with more power at a lower speed. When the strong wind from the pen car blows to the top of the acrylic, the top edge of the acrylic will usually soften to a milky white color.
The trick to fixing this problem is to adjust the air adjustment screw so that as little air as possible is introduced from the compressor.
3. Align with the center point of the acrylic
Operate the autofocus process on top of the acrylic. Manually move the table up 1/3 or even half the thickness of the material.
The worktable moves upward by 3-15 mm, which is equivalent to 1/3 of the material thickness, and by 15-30 mm, which is equivalent to half of the material thickness.
4. A powerful exhaust stream is created at the base of the heavy acrylic
A good exhaust system is the first condition for a good working environment. The purpose of the air flow is to pull out the flammable gas to prevent the flame at the bottom of the acrylic.
Use smart box or cutting box as the air flow carrier. Place a thin sheet of aluminum foil or sheet on the grid table to cover the entire work area. The acrylic should be about 2-10cm above the grid table.
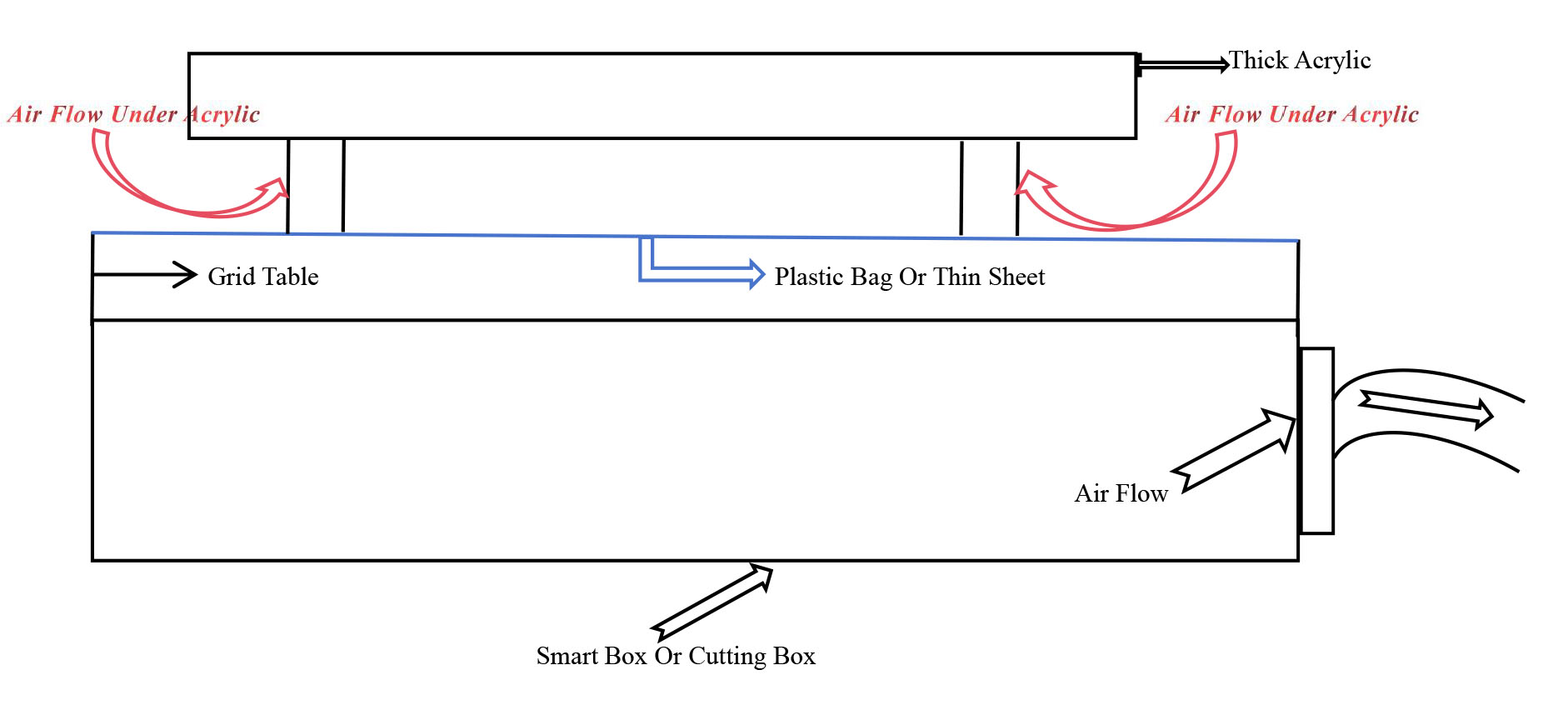
5. Use high resolution parameters
When cutting thick acrylic sheets, resolution is a key factor, and the DPI (Dots Per Inch) parameter must be set to 1000 or above. In addition, PPI (Pulse Per Inch) must all be set to “X”.